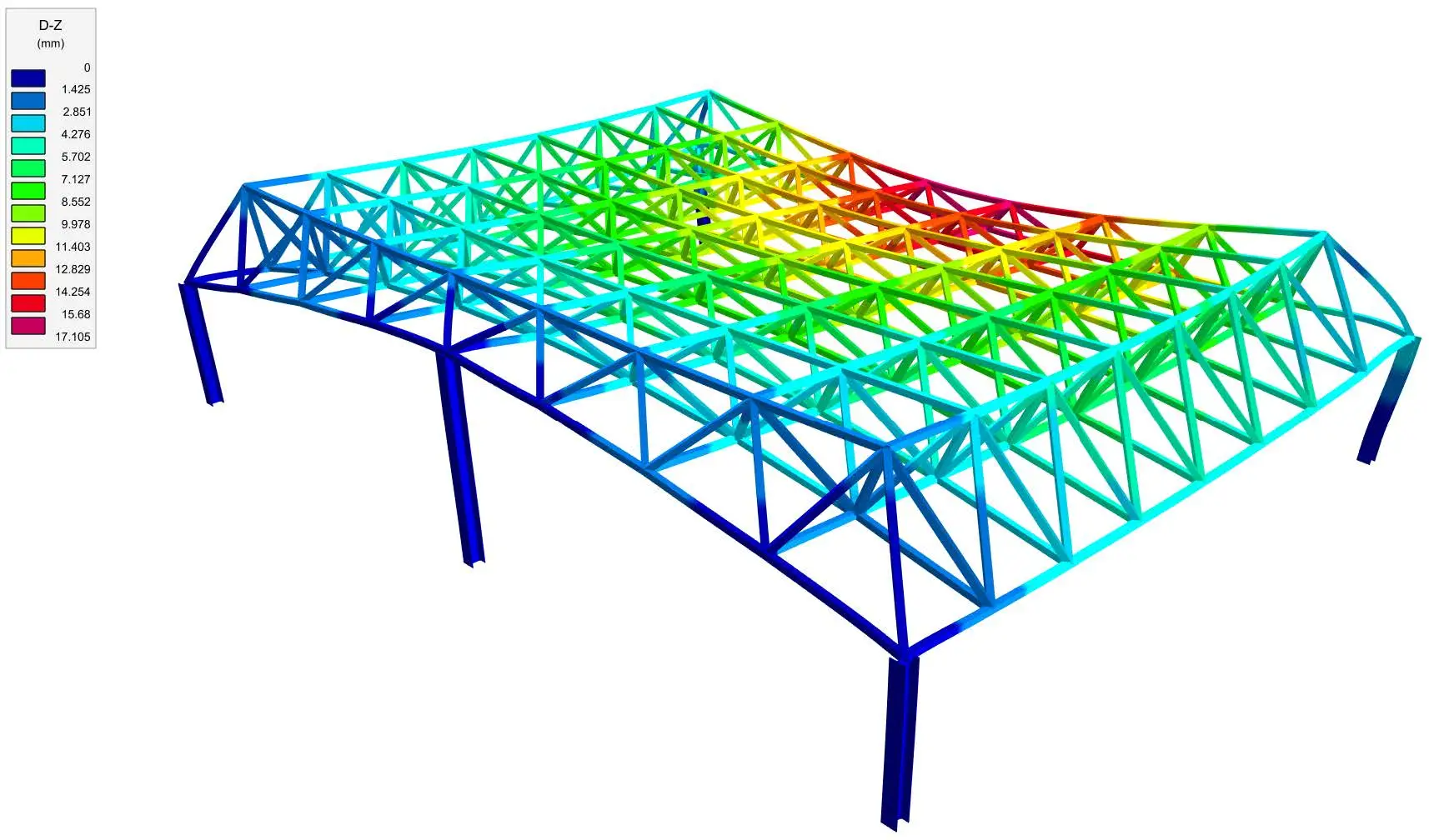
Space Trusses
Summary
Space Truss Design in ProtaStructure 2025 serves as the three-dimensional counterpart of planar trusses. Space trusses consist of straight members connected at their ends, forming a robust framework. These members can be made of steel, aluminum, or other materials depending on project needs. Typically, joints in space trusses use ball-and-socket connections. This allows for rotational freedom and helps the truss adapt to different load conditions, maintaining structural integrity.
ProtaStructure 2025 features a Space Truss Macro that simplifies the design process. Users can specify a region and insert a space truss parametrically. The macro offers extensive customization options, including cell size, the number of rows and columns, curvature, and more. This flexibility enables engineers to create precise, adaptable designs tailored to each project’s unique requirements.
The capabilities of Space Truss Design in ProtaStructure 2025 extend beyond initial insertion. Engineers can modify framing types, change member profiles, and apply various loads to space trusses. This ensures an accurate representation of real-world conditions and optimizes load distribution and stability. The parametric approach reduces manual work, minimizes errors, and enhances design efficiency.
In the attached document, you will find detailed instructions on inserting a space truss, changing profiles, applying loads, and more. It offers a user-friendly solution that demonstrates ProtaStructure’s commitment to modern structural engineering tools.
Explore how Space Truss Design can enhance your projects. Achieve maximum design flexibility and precision with the comprehensive capabilities offered. For further details, refer to the “ProtaStructure 2025 New Features” document.